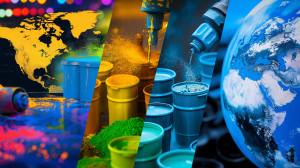
Powder Coating: Market Size & Trends
Introduction The global powder coating market has been experiencing substantial growth, driven by their extensive use across various industries and ...
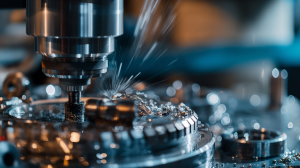
Global Metal Finishing Market: Trends and Growth Opportunities
The global metal finishing market is experiencing significant growth and transformation, driven by advancements in technology, increasing demand from various ...
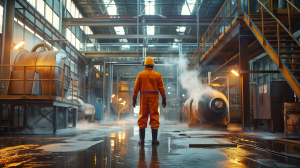
Benefits of Powder Coating: A Comprehensive Guide
Introduction The Benefits of Powder coating has become an essential process in the manufacturing of industrial products, offering superior finishes, ...
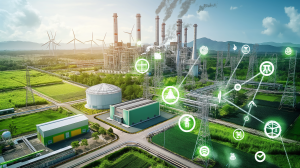
Sustainability in Metal Finishing: Innovations for a Greener Future
Introduction Sustainability is becoming a critical focus across industries as the world faces increasing environmental challenges. The metal finishing industry, ...
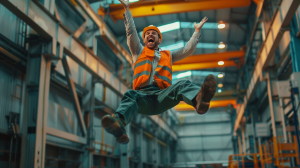
Customer Success Stories
The Importance of Customer Success Customer success stories is the cornerstone of AFAC Ltd's mission. We believe that our growth ...
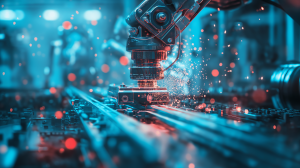
Quality Metal Finishing: Masking Solutions Boost Efficiency
Introduction The metal finishing industry has seen significant advancements over the years, with innovations in masking solutions playing a crucial ...
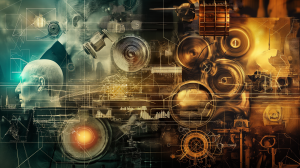
Evolution of Metal Finishing: Methods to Modern Innovations
The evolution of metal finishing in the industry has seen significant advancements over the centuries, evolving from rudimentary techniques to ...
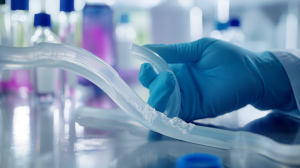
Silicone Rubber Applications
The Industrial and Consumer Markets Introduction to Silicone Rubber applications Silicone rubber is a synthetic elastomer known for its exceptional ...
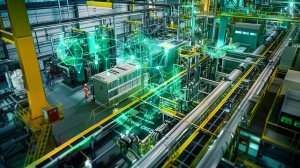
The Future of Manufacturing: UK and Beyond
Introduction Manufacturing has long been the backbone of economies around the world, driving growth, innovation, and job creation. As we ...
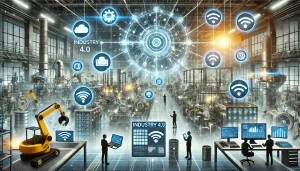
Preparing for Industry 4.0:
Future-Proofing Your Manufacturing Business; Understanding Industry 4.0 and Its Significance Industry 4.0, often referred to as the Fourth Industrial Revolution, ...
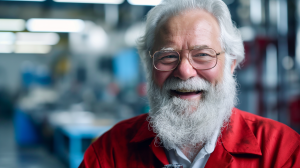
AFAC Ltd: Celebrating Over 40 Years of Excellence in Masking Solutions
Introduction to AFAC Ltd and Its Founders Since its inception in 1980, AFAC Ltd has carved a niche in the ...
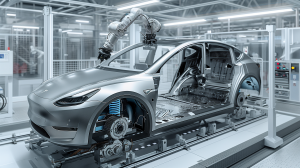
Powder Coating in Electric Vehicles (EVs)
Introduction The electric vehicle (EV) market is set for exponential growth in the coming years, driven by increasing consumer demand, ...