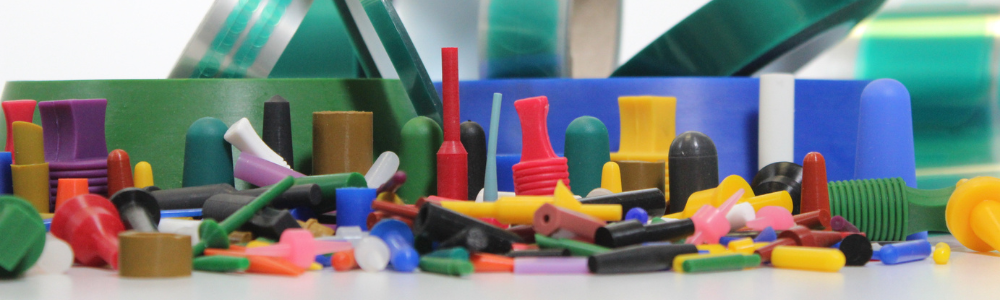
Powder coating is a popular finishing technique for various metal products due to its durability, appearance, and cost-effectiveness. However, proper masking is essential to ensure that the coating only covers the desired areas and maintains the product’s functionality. In this article, we will discuss several tips and tricks for masking during powder coating to achieve optimal results.
1. Understand the Powder Coating Process
Before masking a metal product, it’s crucial to understand the powder coating process. This includes the type of coating, the curing process, and the temperature required for the process. This knowledge can help determine the appropriate masking materials, techniques, and placement.
2. Choose the Right Masking Materials
The type of masking materials used depends on the product’s size, shape, and complexity. Common masking materials include tapes, plugs, caps, and films. High-temperature masking materials, such as silicone tapes, are suitable for products that undergo high temperatures during the powder coating process. Selecting the right masking materials can help prevent leakage, overspray, and defects.
3. Clean and Prepare the Surface
Proper surface preparation is critical before masking a product. The surface should be thoroughly cleaned to remove any contaminants that could affect the powder coating’s adhesion. The product should also be free from oil, grease, rust, and other impurities. A clean surface helps the masking materials adhere correctly and prevents defects during the coating process.
4. Use Precision Tools
To achieve accurate masking, it’s essential to use precision tools such as cutting knives, scissors, and hole punches. These tools help create precise shapes and sizes of masking materials that conform to the product’s contours. Precision tools also make it easier to remove masking materials after the coating process, minimizing the risk of damage to the product.
5. Consider the Product’s Positioning
The product’s positioning during the coating process can affect the masking requirements. For example, if the product hangs during the coating process, masking materials such as plugs and caps should cover the product’s interior to prevent coating penetration. If the product is flat, tapes and films are suitable for covering the surface areas that require masking.
6. Pay Attention to Overlapping Areas
Overlapping areas can occur when using multiple masking materials, such as tapes and plugs, to cover a product. These areas can create a gap that exposes the product to the coating process, resulting in defects. To prevent this, ensure that the masking materials overlap precisely and create a seamless cover.
7. Test Masking Materials
Testing masking materials before the coating process can help identify any defects or limitations. This includes testing the masking materials’ temperature resistance, adhesion, and flexibility. Testing can also help determine the appropriate thickness and coverage of the masking materials.
8. Remove Masking Materials Carefully
After the coating process, it’s crucial to remove the masking materials carefully to prevent damage to the product. This includes using precision tools to remove the masking materials and avoiding sharp objects that could scratch or damage the product’s surface.
9. Inspect the Product
After removing the masking materials, inspect the product for defects, overspray, or coating thickness. Any defects should be addressed before the product is delivered to the customer. Proper inspection can help ensure that the product meets the required quality standards.
10. Train Employees on Proper Masking Techniques
Proper training of employees on masking techniques is essential to ensure consistent and high-quality results. Training should include the types of masking materials, their appropriate use, and the masking process. Employees should also be aware of the potential risks, such as defects and overspray, and how to prevent them.
In conclusion, masking is a crucial step in achieving optimal results during powder coating. Following the tips and tricks discussed above can help prevent defects, overspray, and ensure that the product meets the required quality standards. Understanding the powder coating process, choosing the right masking materials, cleaning and preparing the surface, using precision tools, considering the product’s positioning, paying attention to overlapping areas, testing masking materials, removing masking materials carefully, inspecting the product, and training employees on proper masking techniques are essential for successful powder coating.
By following these steps, you can ensure that the powder coating process is efficient and effective, resulting in a high-quality finish that meets the product’s requirements. Proper masking can also save time and money by reducing the need for touch-ups and rework.
Masking Tips & Tricks: Frequently Asked Questions:
- What is powder coating, and how does it differ from traditional painting?
- Powder coating is a finishing technique that uses a dry powder applied electrostatically and then cured under heat to create a durable and uniform finish. Unlike traditional painting, powder coating does not require solvents, which can release volatile organic compounds (VOCs) into the atmosphere.
- Can any metal product be powder coated?
- Yes, most metal products can be powder coated, including aluminum, steel, brass, and copper.
- What are some common masking materials used during powder coating?
- Common masking materials include tapes, plugs, caps, and films. High-temperature masking materials, such as silicone tapes, are suitable for products that undergo high temperatures during the powder coating process.
- What tips are there for how can I prevent defects during the powder coating process?
- Proper masking, cleaning and preparing the surface, using precision tools, and inspecting the product after coating can help prevent defects during the powder coating process.
- Why is employee training essential for proper masking during powder coating?
- Employee training is essential to ensure consistent and high-quality results. Employees should be aware of the potential risks, such as defects and overspray, and how to prevent them. Training should include the types of masking materials, their appropriate use, and the masking process.
- Can I reuse masking materials?
- Reusing masking materials is not recommended, as they can lose their adhesive properties or become damaged during the coating process. Using new masking materials for each coating process ensures optimal results and prevents defects.
- How do I know if the product is ready for powder coating?
- Before masking and coating the product, it’s essential to ensure that the surface is clean, free from oil, grease, rust, and other impurities. Testing the surface with a water break test or a solvent wipe can help determine if the surface is ready for powder coating.
- What should I do if I encounter a defect after coating?
- If you encounter a defect after coating, you should inspect the product and determine the cause of the defect. This may involve removing the coating, addressing the defect, and recoating the product. Preventative measures, such as proper masking and surface preparation, can also help prevent defects.
- How long does powder coating last?
- Powder coating can last for many years, depending on the product’s environment and usage. Proper maintenance and care can extend the life of the coating, such as avoiding abrasive cleaning methods and harsh chemicals.
- Can I apply multiple colors or finishes during powder coating?
- Yes, multiple colors or finishes can be applied during powder coating by using different masking materials for each color or finish. This allows for precise application and creates a unique and customized product.
Summing up masking tips & tricks.
Overall, proper masking during powder coating is critical to achieving a high-quality and durable finish. By following the tips and tricks discussed in this article and training employees on proper masking techniques, you can ensure consistent and successful powder coating results. Remember to choose the right masking materials, clean and prepare the surface, use precision tools, consider the product’s positioning, test masking materials, remove masking materials carefully, inspect the product, and train employees on proper masking techniques.