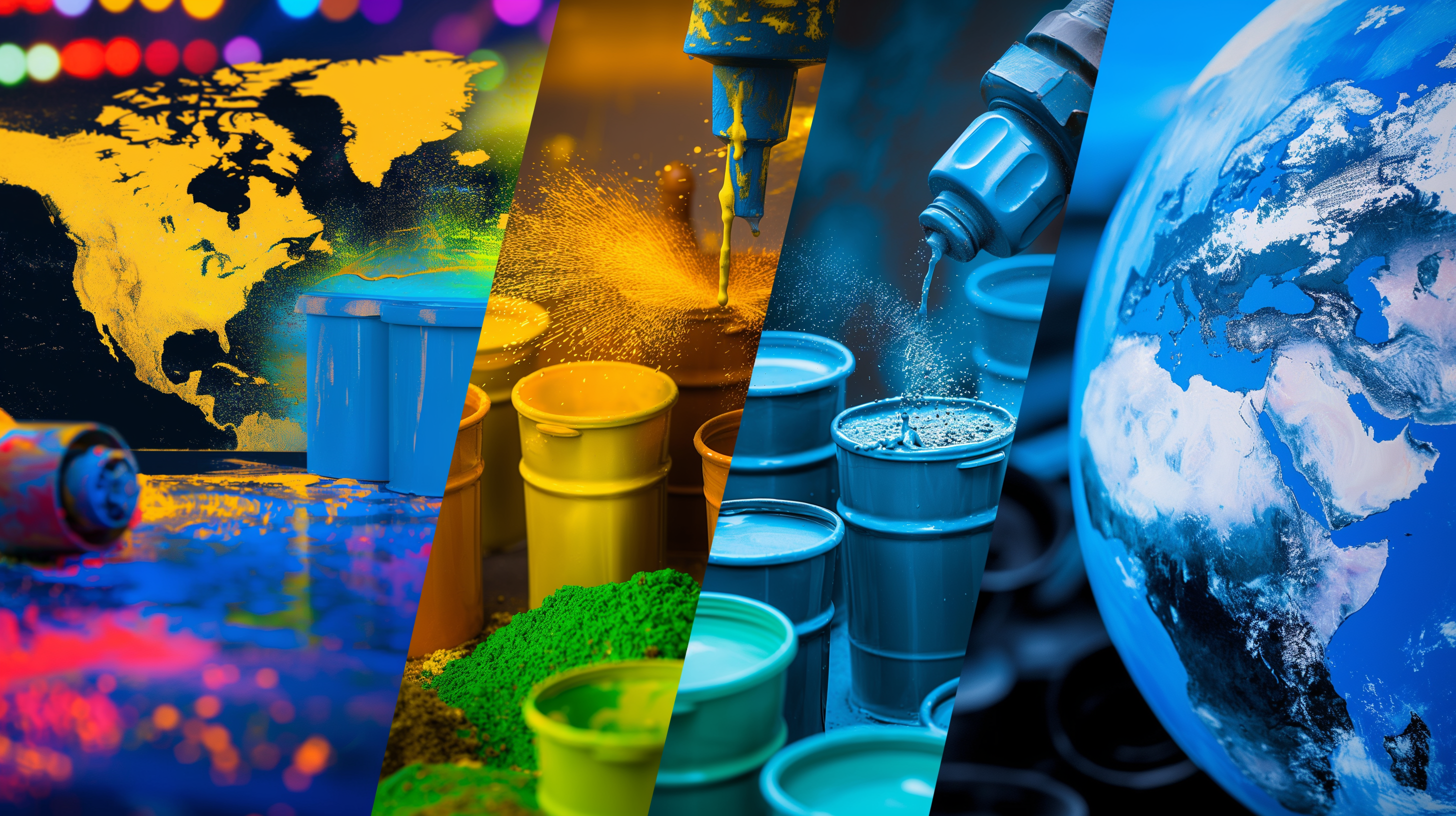
Introduction
The global powder coating market has been experiencing substantial growth, driven by their extensive use across various industries and the numerous advantages they offer over traditional paints and coatings. This article provides an in-depth analysis of the powder coatings market size, key trends, and growth projections, highlighting the factors contributing to their increasing popularity in sectors such as appliances, automotive, infrastructure, and general industrial applications.
Powder Coating: Market Size and Growth Projections
Current Market Size
As of 2023, the global powder coatings market was valued at approximately USD 10.39 billion. This significant market size reflects the widespread adoption of powder coatings in numerous industries, thanks to their superior performance characteristics and environmental benefits.
Future Growth Projections
The powder coatings market is projected to grow at a robust compound annual growth rate (CAGR) of 5.8% from 2024 to 2030. This growth trajectory indicates a promising future for the industry, driven by continuous advancements in coating technologies and increasing demand from various end-use sectors.
Powder Coating: Key Trends Driving Market Growth
Widespread Industrial Usage
Powder coatings are extensively used in diverse sectors, each contributing to the market’s growth:
- Appliances: Powder coatings are favored for their durability and aesthetic appeal, making them ideal for household appliances such as refrigerators, washing machines, and ovens.
- Automotive: The automotive industry benefits from powder coatings’ high resistance to heat, impact, and corrosion, enhancing vehicle longevity and appearance.
- Infrastructure: In the infrastructure sector, powder coatings are used for their protective properties, which help extend the lifespan of construction materials exposed to harsh environmental conditions.
- General Industrial Applications: Various industrial equipment and machinery rely on powder coatings for their robust protection and superior finish.
Advantages of Powder Coatings
Powder coatings offer several advantages over conventional paints and coatings, contributing to their growing popularity:
- Uniform Thickness: Powder coatings provide an even coating thickness, ensuring consistent coverage and reducing material waste.
- Superior Appearance: They offer a high-quality finish with a smooth, attractive appearance, enhancing the visual appeal of coated products.
- High Resistance: Powder coatings are highly resistant to heat, impact, and corrosion, making them suitable for demanding applications in harsh environments.
- Environmental Benefits: Unlike liquid paints, powder coatings contain no solvents and release negligible amounts of volatile organic compounds (VOCs), making them environmentally friendly and compliant with stringent environmental regulations.
Powder Coating: Emerging Markets and Growth Opportunities
Asia-Pacific Region
The Asia-Pacific region is expected to be the fastest-growing market for powder coatings, driven by rapid industrialization, infrastructure development, and increasing automotive production in countries like China and India. The region’s favorable regulatory environment and availability of low-cost labor also contribute to its market dominance.
North America and Europe
North America and Europe continue to be significant markets for powder coatings, with strong demand from the automotive, appliances, and construction sectors. The focus on sustainability and stringent environmental regulations further support the adoption of powder coatings in these regions.
Latin America and Middle East & Africa
Emerging markets in Latin America and the Middle East & Africa are also witnessing growth in the powder coatings market. Increasing industrial activities, infrastructure projects, and investments in manufacturing are driving demand in these regions, presenting new growth opportunities for industry players.
Powder Coating: Technological Advancements and Innovations
Powder Coating: Advanced Coating Technologies
Ongoing research and development in coating technologies are leading to innovations that enhance the performance and application of powder coatings. Key advancements include:
- Nano Coatings: Incorporating nanotechnology to improve the durability, scratch resistance, and self-cleaning properties of powder coatings.
- High-Temperature Resistant Coatings: Developing coatings that can withstand extreme temperatures, making them suitable for high-heat applications in automotive and industrial sectors.
- Low-Cure Powder Coatings: Innovations that allow powder coatings to cure at lower temperatures, reducing energy consumption and expanding their application range.
Powder Coating: Sustainable Coatings
The development of sustainable powder coatings is gaining traction, driven by the need to reduce environmental impact and comply with regulatory standards. These coatings are formulated with eco-friendly materials and processes, offering a greener alternative to traditional coatings.
Powder Coating: Competitive Landscape and Key Players
Powder Coating: Major Market Players
The global powder coatings market is highly competitive, with several key players leading the industry. Some of the prominent companies include:
- Akzo Nobel N.V.: Known for its wide range of high-performance powder coatings used in various industries.
- PPG Industries, Inc.: A leading provider of innovative powder coating solutions with a strong focus on sustainability.
- Sherwin-Williams Company: Offers a comprehensive portfolio of powder coatings that cater to diverse applications.
- Axalta Coating Systems: Specializes in advanced powder coatings that provide superior protection and finish.
Powder Coating: Strategic Initiatives
To maintain a competitive edge, market players are focusing on strategic initiatives such as mergers and acquisitions, collaborations, and product innovations. These efforts aim to expand their product offerings, enhance their market presence, and address the evolving needs of customers.
Powder Coating: Strategic Opportunities for AFAC Ltd
Leveraging Market Growth
AFAC Ltd can capitalize on the growing powder coatings market by expanding its product portfolio and catering to the increasing demand from various industries. By investing in research and development, AFAC Ltd can introduce innovative coatings that meet the specific requirements of its clients.
Expanding Geographical Reach
Expanding into emerging markets, particularly in the Asia-Pacific region, can provide significant growth opportunities for AFAC Ltd. Establishing a presence in these high-growth regions will enable the company to tap into new customer bases and increase its market share.
Focusing on Sustainability
With sustainability becoming a key trend in the powder coatings market, AFAC Ltd can differentiate itself by developing eco-friendly coatings and processes. Promoting sustainable practices will not only enhance the company’s reputation but also attract environmentally conscious customers.
Strengthening Customer Relationships
Building and maintaining strong relationships with customers is crucial for long-term success. AFAC Ltd should focus on providing customized solutions, excellent customer service, and ongoing support to foster loyalty and drive repeat business.
Conclusion
The global powder coatings market is poised for significant growth, driven by advancements in technology, increasing demand from key industries, and a focus on sustainability. By understanding market trends and strategically positioning itself, AFAC Ltd can capitalize on the numerous opportunities available in this dynamic industry.
At AFAC Ltd, we are committed to delivering innovative and sustainable powder coating solutions that meet the highest standards of quality and performance. For more information about our products and services, visit AFAC Ltd.