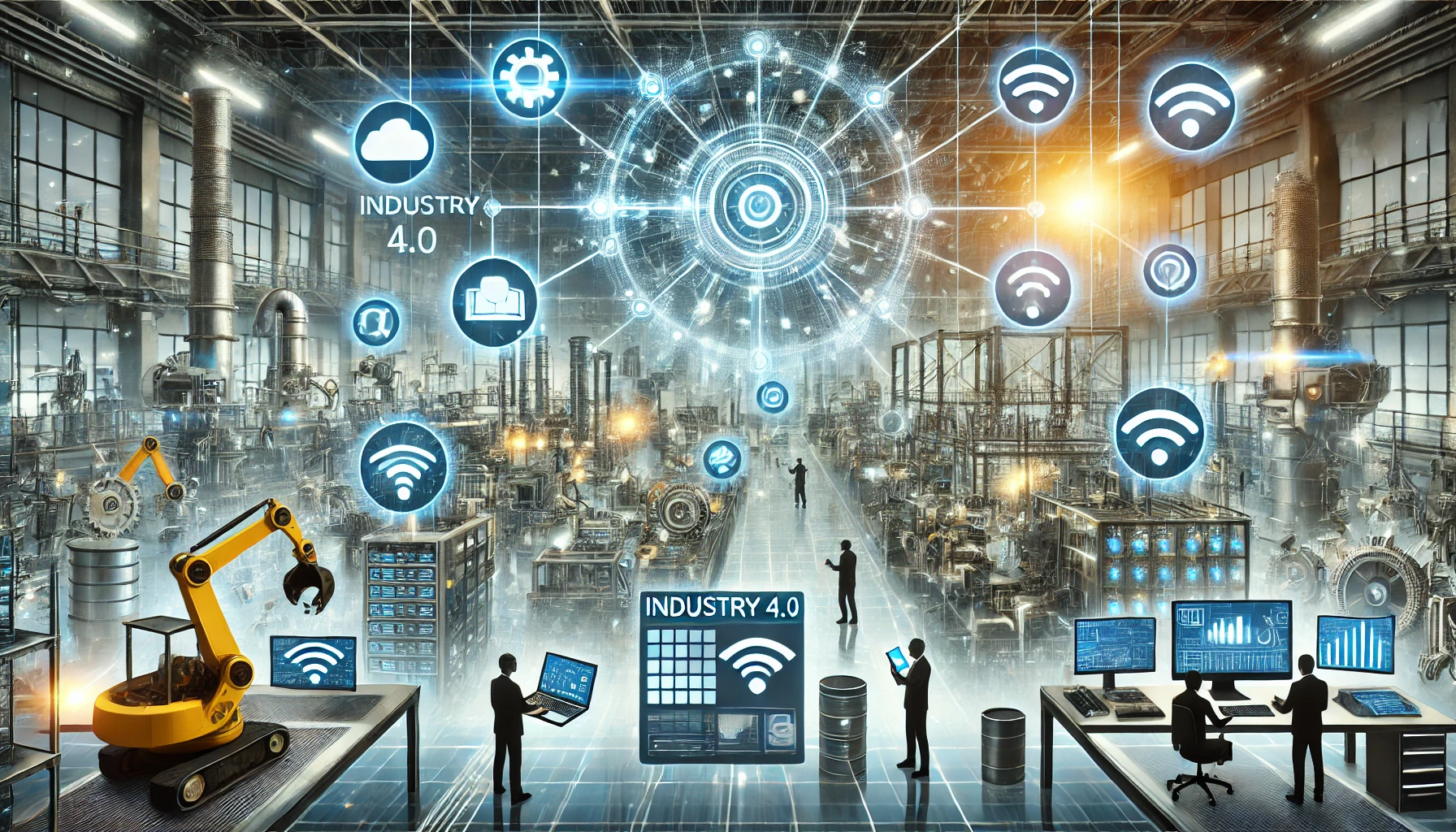
Future-Proofing Your Manufacturing Business; Understanding Industry 4.0 and Its Significance
Industry 4.0, often referred to as the Fourth Industrial Revolution, represents a new era of manufacturing that integrates advanced technologies to create smart, efficient, and flexible production environments. Unlike previous industrial revolutions that focused on mechanization, mass production, and automation, Industry 4.0 leverages digital transformation to connect machines, systems, and people in real-time.
The significance of Industry 4.0 lies in its ability to enhance productivity, optimize processes, reduce costs, and improve product quality. By adopting Industry 4.0 technologies, manufacturers can gain a competitive edge and future-proof their businesses in an increasingly digital world.
Key Technologies of Industry 4.0
Internet of Things (IoT)
IoT refers to the network of interconnected devices that communicate and exchange data. In manufacturing, IoT enables real-time monitoring and control of production processes, predictive maintenance, and efficient resource management.
Artificial Intelligence (AI)
AI enhances decision-making and process optimization through machine learning algorithms and data analytics. AI applications in manufacturing include quality control, predictive maintenance, demand forecasting, and supply chain optimization.
Robotics
Advanced robotics and automation systems increase production efficiency and precision. Collaborative robots (cobots) work alongside human operators, performing repetitive and complex tasks with high accuracy.
Big Data and Analytics
Big data analytics involves processing vast amounts of data to derive actionable insights. In manufacturing, big data helps identify trends, optimize production processes, and improve decision-making.
Cyber-Physical Systems (CPS)
CPS integrates physical processes with digital systems, enabling real-time data collection and feedback. This integration enhances process control, reduces downtime, and improves overall efficiency.
Additive Manufacturing (3D Printing)
Additive manufacturing allows for rapid prototyping and customized production. It reduces waste, shortens production cycles, and enables the creation of complex geometries that are difficult to achieve with traditional methods.
Strategies for Implementing Industry 4.0
Assess Your Current State
Begin by evaluating your existing processes, technologies, and workforce capabilities. Identify areas where digital transformation can provide the most significant impact.
Develop a Clear Vision and Roadmap to achieve Industry 4.0
Define your goals and create a strategic roadmap for implementing Industry 4.0 technologies. Prioritize initiatives based on their potential benefits and feasibility.
Invest in the Right Technologies
Choose technologies that align with your business objectives and provide the most value. Consider scalability, compatibility with existing systems, and potential return on investment.
Build a Skilled Workforce
Equip your workforce with the necessary skills to operate and maintain new technologies. Provide training and development programs to ensure employees can adapt to digital transformation.
Foster a Culture of Innovation
Encourage a culture that embraces change and innovation. Empower employees to contribute ideas and participate in the transformation process.
Collaborate with Partners
Partner with technology providers, research institutions, and other industry players to leverage their expertise and accelerate your digital transformation journey.
Benefits and Challenges of Industry 4.0 Digital Transformation
Benefits
- Increased Efficiency: Automated processes and real-time monitoring reduce downtime and improve productivity.
- Enhanced Quality: AI and machine learning enable predictive quality control, minimizing defects and ensuring consistent product quality.
- Cost Savings: Optimized processes and resource management result in significant cost reductions.
- Agility and Flexibility: Digital technologies allow manufacturers to quickly adapt to changing market demands and customize production.
- Data-Driven Decision Making: Real-time data analytics provide valuable insights for informed decision-making.
Challenges
- Initial Investment: Implementing Industry 4.0 technologies requires significant upfront investment.
- Integration Complexity: Integrating new technologies with existing systems can be complex and time-consuming.
- Cybersecurity Risks: Increased connectivity and data exchange heighten the risk of cyberattacks.
- Skill Gaps: The workforce may lack the skills needed to operate and maintain new technologies, necessitating extensive training.
Best Practices in Industry 4.0
- Start Small and Scale: Begin with pilot projects to test new technologies and demonstrate their value. Gradually scale successful initiatives across the organization.
- Focus on Data: Ensure data quality and availability. Implement robust data management practices to support analytics and decision-making.
- Adopt a Holistic Approach: Consider the entire value chain when implementing Industry 4.0 technologies. Integrate processes from design and production to supply chain and customer service.
- Measure and Optimize: Continuously monitor the performance of implemented technologies and make data-driven adjustments to optimize processes.
Conclusion
Preparing for Industry 4.0 is essential for manufacturing businesses looking to stay competitive in the digital age. By understanding the key technologies, developing a strategic roadmap, and addressing the associated challenges, manufacturers can harness the full potential of digital transformation. At AFAC Ltd, we are committed to embracing Industry 4.0 and supporting our clients in their journey towards smart manufacturing.
For more information about our Industry 4.0 solutions and services, visit AFAC Ltd.