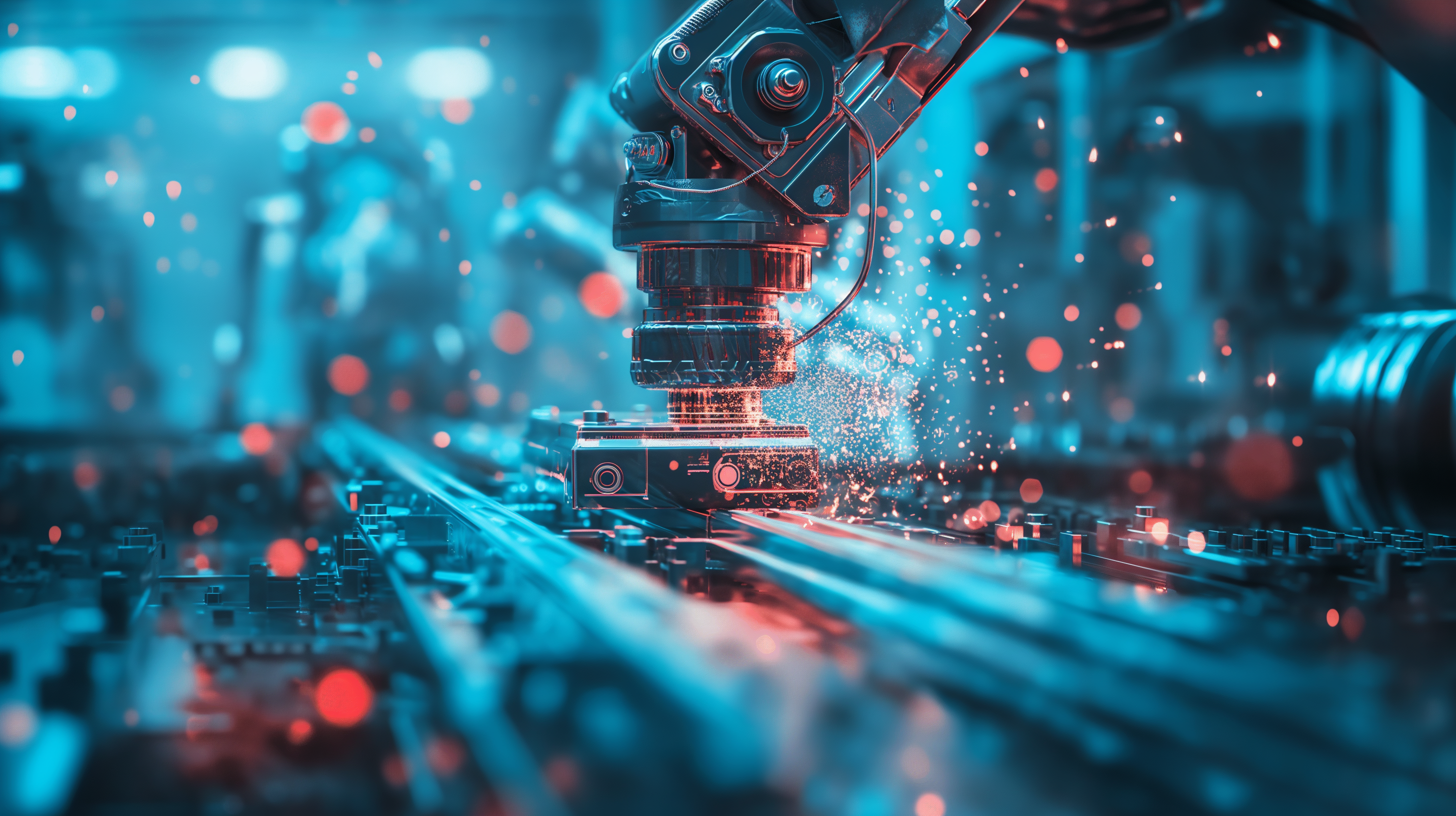
Introduction
The metal finishing industry has seen significant advancements over the years, with innovations in masking solutions playing a crucial role in enhancing efficiency and quality. This article delves into the evolution of masking solutions, from traditional methods to modern technologies, the benefits of advanced masking solutions, real-world applications, and future trends shaping the industry.
Overview of Traditional vs. Modern Masking Solutions
Quality Metal Finishing: Traditional Masking Solutions
Traditional masking solutions have been the backbone of the metal finishing industry for decades. These methods typically involve using tapes, caps, plugs, and liquid masks to protect areas of metal components that should not be coated or treated.
- Tapes and Adhesives: Often used for simple shapes and surfaces, but can be labor-intensive and prone to inconsistencies.
- Caps and Plugs: Suitable for covering holes and threads but may not always provide a perfect seal.
- Liquid Masks: Applied using brushes or spray guns, offering flexibility but requiring significant time for application and drying.
Quality Metal Finishing: Modern Masking Solutions
Modern masking solutions have evolved significantly, driven by advancements in materials and technology. These innovations address the limitations of traditional methods, offering superior performance and efficiency.
- Silicone Rubber Masks: Custom-molded for precise fits, reusable, and highly resistant to high temperatures and chemicals.
- 3D-Printed Masks: Enable the creation of complex shapes and designs tailored to specific components, reducing application time and improving accuracy.
- Magnetic Masks: Provide a quick and secure method for masking areas, especially useful for components with irregular shapes.
New Materials and Technologies in Masking
Advanced Materials
The development of advanced materials has revolutionized masking solutions, providing enhanced durability, flexibility, and resistance.
- High-Temperature Silicones: Capable of withstanding extreme temperatures, ideal for processes like powder coating and anodizing.
- Fluoroelastomers: Offer excellent chemical resistance, suitable for harsh environments and aggressive substances.
- High-Density Polyethylene (HDPE): Durable and cost-effective, used in a variety of masking applications.
Cutting-Edge Technologies
Innovations in technology have also contributed to the efficiency and effectiveness of masking solutions.
- 3D Printing: Enables rapid prototyping and production of custom masks with complex geometries, reducing lead times and costs.
- Laser Cutting: Provides precision and accuracy in creating masks, especially for intricate designs and tight tolerances.
- Smart Materials: Incorporate responsive properties that can adapt to environmental changes, improving the masking process.
Benefits of Advanced Masking Solutions
Improved Efficiency
Advanced masking solutions significantly enhance efficiency in metal finishing processes.
- Reduced Application Time: Custom masks fit perfectly, minimizing the time required for application and removal.
- Reusable Masks: High-quality materials allow for multiple uses, reducing the need for frequent replacements.
- Automation Compatibility: Modern masks are often compatible with automated systems, streamlining production lines.
Enhanced Quality
The precision and reliability of advanced masking solutions lead to superior quality in metal finishing.
- Consistent Results: Custom-fit masks ensure uniform coverage and protection, resulting in consistent finishes.
- Minimized Defects: High-quality materials and precise fits reduce the risk of defects and rework.
- Protection Against Contaminants: Advanced masks provide better sealing, protecting against contaminants and ensuring cleaner finishes.
Real-World Applications and Success Stories
Quality Metal Finishing: Automotive Industry
In the automotive industry, where precision and durability are paramount, advanced masking solutions have made a significant impact.
- Case Study: An automotive manufacturer implemented 3D-printed masks for their complex components, reducing masking time by 50% and achieving a more consistent finish. This innovation also led to a 30% reduction in rework costs.
Quality Metal Finishing: Aerospace Industry
The aerospace industry benefits greatly from high-performance masking solutions due to its stringent quality requirements.
- Case Study: An aerospace company adopted high-temperature silicone masks for their anodizing process. These masks withstood extreme temperatures and provided a perfect seal, resulting in a 40% increase in throughput and a 20% improvement in coating quality.
Quality Metal Finishing: Electronics Industry
Precision masking is crucial in the electronics industry to protect sensitive components during finishing processes.
- Case Study: An electronics manufacturer used laser-cut masks for their printed circuit boards (PCBs). This approach improved accuracy and reduced application time, leading to a 25% increase in production efficiency and a significant reduction in defects.
Future Trends in Masking Solutions
Quality Metal Finishing: Integration of Smart Technologies
The future of masking solutions will likely see the integration of smart technologies to further enhance performance and efficiency.
- Self-Healing Masks: Materials that can repair minor damages automatically, extending the lifespan of masks.
- IoT-Enabled Masks: Incorporating sensors to monitor and optimize the masking process in real-time, improving quality control.
Quality Metal Finishing: Sustainability and Eco-Friendly Materials
As environmental concerns grow, the development of sustainable and eco-friendly masking materials is becoming a priority.
- Biodegradable Masks: Research into biodegradable materials could lead to more environmentally friendly masking solutions.
- Recyclable Materials: Increased use of recyclable materials to reduce waste and promote sustainability in the industry.
Quality Metal Finishing: Customization and Personalization
Advancements in technology will continue to drive the trend towards more customized and personalized masking solutions.
- AI and Machine Learning: Using AI to design and optimize masks based on specific component geometries and finishing requirements.
- Advanced Manufacturing Techniques: Further developments in 3D printing and laser cutting to create highly customized masks with intricate designs.
Conclusion
Innovative masking solutions are transforming the metal finishing industry, boosting efficiency and enhancing quality. From advanced materials and cutting-edge technologies to real-world applications and future trends, the evolution of masking solutions is paving the way for a more efficient and sustainable industry.
At AFAC Ltd, we are committed to staying at the forefront of these innovations, providing our clients with the highest quality masking solutions tailored to their specific needs. Our dedication to excellence ensures that we continue to lead the industry in delivering innovative, efficient, and reliable masking products.
For more information about our innovative masking solutions, visit AFAC Ltd.