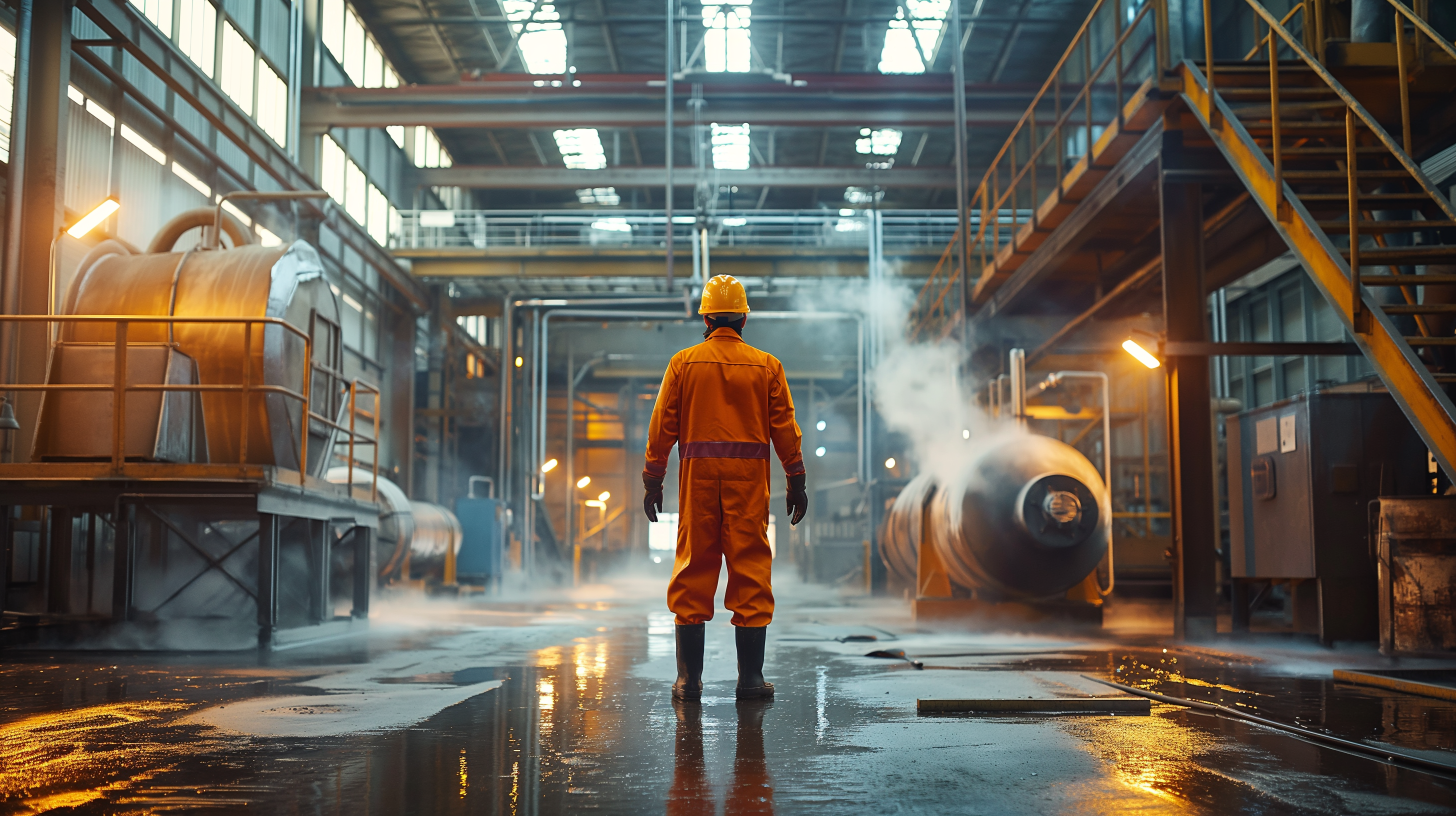
Introduction
The Benefits of Powder coating has become an essential process in the manufacturing of industrial products, offering superior finishes, durability, and cost-effectiveness. This guide delves into the benefits, processes, and applications of powder coatings in the industrial sector, highlighting how they enhance product quality and efficiency.
Benefits of Powder Coatings: For Industrial Products
Superior Finish and Aesthetics
Powder coatings provide a wide range of colors and surface effects, allowing manufacturers to achieve an excellent look and feel for their products. The coatings deliver a uniform thickness, ensuring a smooth and attractive finish that enhances the visual appeal of the coated surfaces.
Long-Lasting Durability
One of the key advantages of powder coatings is their durability. These coatings are highly resistant to heat, impact, and corrosion, which makes them ideal for industrial applications where long-lasting protection is crucial. This durability reduces the need for frequent maintenance and replacement, saving time and costs.
Economic Efficiency
Powder coating is an economically efficient process. It maximizes material usage, as the overspray can be collected and reused, leading to minimal waste. Additionally, the curing process is faster than traditional liquid coatings, which reduces production times and operational costs.
Sustainable Use of Resources
Powder coatings are environmentally friendly, containing no volatile organic compounds (VOCs). This reduces air pollution and makes the process safer for workers and the environment. The efficient use of materials and the recyclability of powder coatings further contribute to sustainable manufacturing practices.
Benefits of Powder Coating: Process in Industrial Applications
Pre-Treatment
The quality of the powder coating largely depends on the pre-treatment of the workpiece. Pre-treatment involves cleaning and preparing the surface to ensure optimal adhesion of the coating. Common pre-treatment methods include:
- Sandblasting: Removes rust, scale, and other contaminants from the surface.
- Chemical Preparation: Uses grease-dissolving agents to clean the surface and apply corrosion protection if needed.
For workpieces requiring high corrosion resistance, a basic wet chemical corrosion protection layer is often applied before powder coating.
Application
Powder coating requires an electrically conductive substrate, making metals ideal candidates. However, other materials such as wood and plastics can also be coated after being made conductive. The application process involves:
- Grounding the Workpiece: The workpiece is electrically grounded to attract the charged powder particles.
- Charging the Powder: There are two primary methods for charging powder:
- Corona Charging: Powder is charged using a high-voltage cascade built into the powder gun.
- Tribo Charging: Powder is charged through friction with bodies in the gun.
Corona charging is more common due to its flexibility in adjusting to different conditions and requirements. Tribo charging is preferred for achieving very smooth surfaces or coating workpieces with complex geometries.
Cross-Linking and Drying (Curing)
After application, the powder-coated layer is cured by heating it to temperatures between 160 and 200 degrees Celsius. The heat causes the powder to melt and form a continuous film, which then hardens into a durable coating. Some powders, known as low-temperature powders, cure at lower temperatures (130-140 degrees Celsius), offering energy savings but requiring careful handling to maintain their integrity during production, transport, and storage.
Benefits of Powder Coating
Standard Products and Customised Solutions
We provide highly efficient standard products as well as customised solutions tailored to specific applications. Whether for manual coating or automated production lines, our offerings ensure versatile application possibilities and efficient process technology.
Efficient Process Technology
Our systems facilitate fast color changes, efficient powder feeding, application, and recovery processes. This ensures high productivity and minimal downtime, making them ideal for both small-scale and large-scale industrial operations.
Support and Expertise
Our specialists offer valuable support throughout the planning and implementation stages, ensuring that all processes are well-coordinated to achieve the desired production output. This includes optimising the coating area per hour or hangers per hour metrics.
Benefits of Powder Coating: Real-World Applications
Benefits of Powder Coatings: Automotive Industry
Powder coatings are extensively used in the automotive industry for coating wheels, underbody components, and other parts that require high durability and corrosion resistance. The uniform finish and long-lasting protection provided by powder coatings enhance the performance and aesthetics of automotive components.
Benefits of Powder Coatings: Appliance Manufacturing
Household appliances benefit from powder coatings due to their attractive finishes and resistance to wear and tear. Appliances such as refrigerators, washing machines, and ovens are commonly powder coated to ensure durability and a high-quality appearance.
Benefits of Powder Coatings: Infrastructure and Construction
In the infrastructure and construction sectors, powder coatings are used to protect structural components from harsh environmental conditions. This includes coating steel beams, fences, and other metal structures to prevent rust and corrosion, extending their lifespan and maintaining their structural integrity.
Benefits of Powder Coating: Future Trends and Innovations
Benefits of Powder Coatings: Advanced Coating Technologies
Ongoing research and development in powder coating technologies are leading to innovative solutions that enhance performance and application versatility. Key advancements include:
- Nano Coatings: These coatings improve scratch resistance, durability, and self-cleaning properties.
- High-Temperature Resistant Coatings: Designed to withstand extreme temperatures, making them suitable for high-heat applications.
- Low-Cure Powder Coatings: These coatings cure at lower temperatures, reducing energy consumption and expanding their application range.
Benefits of Powder Coatings: Increased Sustainability
As sustainability becomes a key focus in manufacturing, powder coatings are evolving to meet environmental standards. The development of eco-friendly materials and processes will continue to drive the adoption of powder coatings in various industries.
Benefits of Powder Coatings: Digitalisation and Automation
The integration of digital technologies and automation in powder coating processes will enhance efficiency, precision, and consistency. Automated systems with real-time monitoring capabilities will enable manufacturers to optimize their coating operations and reduce waste.
Conclusion
Powder coating is a vital process for industrial products, offering superior finishes, durability, and economic efficiency. The ongoing advancements in powder coating technologies and the growing emphasis on sustainability make it an increasingly attractive option for manufacturers. At AFAC Ltd, we are committed to providing high-quality powder coating solutions that meet the diverse needs of our clients while promoting sustainable manufacturing practices.
For more information about our powder coating services and solutions, visit AFAC Ltd.