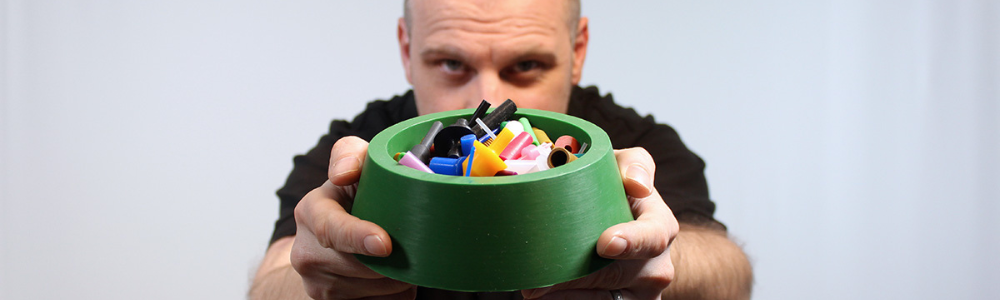
Metal finishing processes like powder coating, electroplating, and anodising are crucial in enhancing the aesthetics and durability of metallic surfaces. During these processes, masking products for metal finishing are used to protect specific areas of the metal that are not intended to be coated, plated or anodised. This is essential in achieving the desired finish and preventing damage or unwanted coating on certain parts of the metal.
This article will provide a comprehensive guide on masking products for metal finishing including powder coating, electroplating, and anodising. We will discuss the various types of masking products available, their applications, and their advantages and disadvantages.
Types of Masking Products Used During Metal Finishing:
Masking products are available in various forms, depending on the nature of the metal finishing process. Here are some of the common types of masking products used during metal finishing:
- Masking Tapes: These are adhesive tapes that can be easily applied and removed from surfaces. They are available in different widths and lengths and can be used for masking large or small areas.
- High-Temperature Tapes: These are special masking tapes designed for use during high-temperature metal finishing processes like powder coating. They can withstand temperatures of up to 300°C and are ideal for masking areas that require high-temperature resistance.
- Masking Caps: These are caps that are used to cover specific areas of a metal surface, like threaded holes or studs, that need to be protected from coating or plating.
- Silicone Plugs: These are flexible silicone plugs that are used to mask off holes and other irregular shapes on a metal surface. They are ideal for use during anodising and other chemical finishing processes.
- Powder Coating Masks: These are specifically designed masks that can be used for powder coating. They are made from materials that can withstand high temperatures and can be customised to fit specific shapes.
Masking Products Used During Powder Coating:
Powder coating is a popular metal finishing process that involves spraying a dry powder onto a metal surface and then baking it to form a durable and protective coating. Here are some of the masking products used during powder coating:
High-Temperature Tapes: These tapes can be used to mask areas that need to be protected from coating. They are ideal for use during high-temperature powder coating processes.
Powder Coating Masks: These are specially designed masks that can be used to cover specific areas of a metal surface that do not require coating. They can be customised to fit specific shapes and are made from materials that can withstand high temperatures.
Silicone Plugs: These are ideal for masking threaded holes, studs, and other irregular shapes on a metal surface that need to be protected from coating.
Masking Products Used During Electroplating
Electroplating is a metal finishing process that involves the deposition of a thin layer of metal onto a substrate using an electric current. The process enhances the durability and appearance of the metal surface, but it also requires precision masking to ensure that only the intended areas are electroplated. In this section, we will discuss the different types of masking products used during electroplating.
Electroplating Tapes:
Electroplating tapes are specially designed masking tapes that can withstand the harsh chemicals and high temperatures involved in electroplating. They are resistant to the acidic and caustic solutions used during the process, ensuring that they do not dissolve or break down during electroplating.
These tapes are available in different widths and lengths, making them ideal for masking large or small areas. They are easy to apply and remove and do not leave any residue or damage to the surface of the metal.
High-Temperature Tapes:
High-temperature tapes are masking tapes that are specially designed for use in high-temperature environments. They can withstand temperatures of up to 260°C, making them ideal for use during electroplating, which involves heating the metal substrate to a high temperature.
These tapes are available in different sizes and shapes and are ideal for masking off areas that do not require electroplating. They are easy to apply and remove and do not leave any residue or damage to the surface of the metal.
Masking Caps and Plugs:
Masking caps and plugs are used to cover specific areas of a metal surface, such as threaded holes or studs, that need to be protected from electroplating. They are available in different sizes and shapes, making them ideal for masking off irregular shapes.
Masking caps and plugs are made from materials that can withstand the chemicals and high temperatures involved in electroplating. They are easy to apply and remove and do not leave any residue or damage to the surface of the metal.
Conductive Masks:
Conductive masks are used to mask specific areas of the metal surface that require a different electroplating process than the rest of the surface. They are made from a conductive material, usually graphite, and are applied to the surface using an adhesive.
Conductive masks allow for precise masking of complex shapes and are ideal for use in electroplating processes that require different types of electroplating in different areas of the metal surface.
Masking products used during anodising
Anodizing is an electrochemical process that is used to create a protective oxide layer on the surface of a metal. The process involves immersing the metal in an electrolytic solution and passing an electric current through it to stimulate the growth of the oxide layer. Anodizing can enhance the durability and appearance of the metal surface, but it also requires precise masking to ensure that only the intended areas are anodized. In this section, we will discuss the different types of masking products used during anodizing.
- Anodizing Tapes:
Anodizing tapes are specially designed masking tapes that can withstand the harsh chemicals and high temperatures involved in anodizing. They are resistant to the acidic and caustic solutions used during the process, ensuring that they do not dissolve or break down during anodizing.
These tapes are available in different widths and lengths, making them ideal for masking large or small areas. They are easy to apply and remove and do not leave any residue or damage to the surface of the metal.
- High-Temperature Tapes:
High-temperature tapes are masking tapes that are specially designed for use in high-temperature environments. They can withstand temperatures of up to 260°C, making them ideal for use during anodizing, which involves heating the metal substrate to a high temperature.
These tapes are available in different sizes and shapes and are ideal for masking off areas that do not require anodizing. They are easy to apply and remove and do not leave any residue or damage to the surface of the metal.
- Masking Dots:
Masking dots are small, adhesive-backed dots that are used to mask specific areas of a metal surface that require protection during anodizing. They are available in different sizes and shapes, making them ideal for masking off irregular shapes.
Masking dots are made from materials that can withstand the chemicals and high temperatures involved in anodizing. They are easy to apply and remove and do not leave any residue or damage to the surface of the metal.
- Liquid Masking:
Liquid masking is a masking technique that involves applying a liquid masking material to the metal surface using a brush, spray, or roller. The liquid masking material is typically a latex-based compound that dries to form a protective film.
Liquid masking is ideal for masking irregular shapes and can be used in conjunction with other masking techniques such as anodizing tapes and masking dots. The liquid masking material is easy to apply and remove and does not leave any residue or damage to the surface of the metal.
Advantages & disadvantages of masking products
Masking products are essential tools in metal finishing processes such as powder coating, electroplating, and anodizing. They are used to protect specific areas of a metal surface from being treated, ensuring that only the desired areas are affected. In this section, we will discuss the advantages and disadvantages of masking products.
Advantages:
- Precision: Masking products are designed to create precise and accurate boundaries between treated and untreated areas. This level of precision ensures that the intended areas are protected from damage and that the desired outcome of the metal finishing process is achieved.
- Versatility: Masking products are available in various types, including tapes, dots, and liquid masks. This versatility allows for the masking of a wide range of shapes and sizes, making them suitable for use in complex and intricate metal finishing projects.
- Time-saving: Masking products are easy to apply and remove, making them a time-saving tool for metal finishing processes. They allow for efficient masking of large or small areas, reducing the amount of time spent on the masking process.
- Cost-effective: The use of masking products is a cost-effective solution for metal finishing processes. By using masking products, the need for additional treatments or rework is reduced, resulting in cost savings.
Disadvantages:
- Residue: Some masking products may leave a residue on the surface of the metal after the masking process, which can affect the appearance of the finished product.
- Adhesion: The adhesion of masking products can vary depending on the type and quality of the product used. Poor adhesion can result in the product peeling or coming off during the metal finishing process.
- Compatibility: Some masking products may not be compatible with specific metal finishing processes, such as high-temperature processes or processes that require the use of harsh chemicals.
- Labor-intensive: The application and removal of masking products can be a labor-intensive process, especially in complex and intricate metal finishing projects.
FaQs about masking products used during metal finishing
In this section, we will answer some frequently asked questions about masking products used during metal finishing.
Q: What are masking products used for in metal finishing processes? A: Masking products are used to protect specific areas of a metal surface from being treated during metal finishing processes such as powder coating, electroplating, and anodizing. They ensure that only the intended areas are affected, resulting in precise and accurate finishes.
Q: What are the different types of masking products? A: There are various types of masking products, including tapes, dots, and liquid masks. Each type has specific properties and applications, making them suitable for use in different metal finishing projects.
Q: How do you select the appropriate masking product for a metal finishing project? A: The selection of the appropriate masking product depends on several factors, including the type of metal being finished, the metal finishing process being used, the size and shape of the areas to be masked, and the level of precision required. It is essential to consult with a professional or supplier to select the appropriate masking product for the project.
Q: Can masking products be reused? A: The reuse of masking products depends on the type and quality of the product used. Some products, such as tapes and dots, are designed for single-use only, while others, such as liquid masks, can be reused.
Q: What are some tips for applying masking products? A: When applying masking products, it is essential to ensure that the surface is clean and free of debris, the masking product is applied evenly, and any air pockets or bubbles are eliminated. It is also crucial to follow the manufacturer’s instructions and use appropriate safety equipment, such as gloves and goggles.
Q: Are masking products environmentally friendly? A: The environmental impact of masking products depends on the type and quality of the product used. Some masking products are biodegradable, while others are not. It is essential to select masking products that are environmentally friendly and dispose of them appropriately.
Conclusion:
Masking products play a vital role in metal finishing processes, providing precise and accurate masking of specific areas of a metal surface. The selection of the appropriate masking product depends on several factors, including the type of metal being finished, the metal finishing process being used, and the level of precision required. It is crucial to follow manufacturer’s instructions and use appropriate safety equipment when applying masking products. The environmental impact of masking products should also be considered, and environmentally friendly products should be selected and disposed of appropriately.