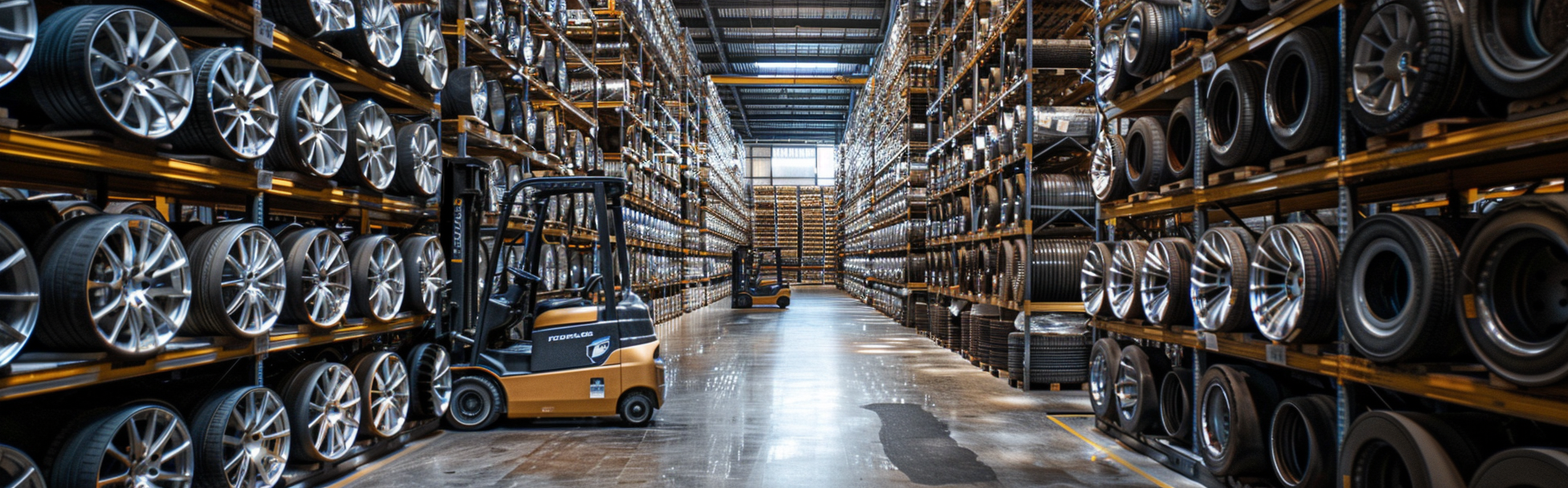
Welcome to another case study with AFAC Custom Masking Solutions. Today, we are excited to highlight a specially developed pull plug designed for a European wheel manufacturer. This case study focuses on the application and benefits of this custom solution in the manufacturing of wheels for large vehicles.
The Challenge
The client, a prominent European manufacturer of alloy and steel wheels for large vehicles, faced a critical challenge in their powder-coating process. Ensuring a powder-free chamfer on the wheels was essential for safety, as it allowed for accurate metal-to-metal contact when bolts were torqued. Any powder build-up on the chamfer could lead to powder cracking, resulting in inaccurate torque settings and potential wheel failure, posing significant safety risks.
Our Solution
To address this issue, AFAC developed a custom pull plug specifically designed to protect the chamfer on alloy and steel wheels during the powder-coating process. Here are the key features of our solution:
- Effective Protection: The pull plug provides robust protection for the chamfer, preventing any powder build-up during the coating process.
- Ease of Use: Designed for easy installation and removal, the pull plug ensures a seamless fit, which enhances efficiency on the production line.
- Durability: Made from high-quality materials, the pull plug is durable and withstands the rigorous conditions of the manufacturing environment, ensuring long-term usability.
Implementation and Results
The custom pull plug was successfully integrated into the client’s manufacturing process, yielding significant improvements in safety and efficiency. Here’s how it impacted their operations:
- Safety Enhancement: By preventing powder build-up on the chamfer, the pull plug ensured accurate metal-to-metal contact, eliminating the risk of powder cracking and potential wheel failure.
- Reliability: The precise protection provided by the pull plug contributed to more reliable torque settings, enhancing the overall safety of the wheels.
- Efficiency: The easy-to-use design of the pull plug streamlined the production process, reducing downtime and increasing throughput.
Client Feedback
The client was highly satisfied with the custom pull plug solution provided by AFAC. They appreciated the significant improvement in the safety and reliability of their wheels. The efficiency gains in their production process were also noted as a major benefit, as it allowed for smoother operations and reduced potential for error.
Conclusion
This case study showcases AFAC’s commitment to developing custom solutions that address specific challenges in manufacturing processes. By designing a pull plug that effectively protects the chamfer on wheels, we were able to enhance both safety and reliability for our client in the heavy machinery sector.
If you are a quality manager, production manager, or product designer looking for custom masking solutions to improve your manufacturing processes, AFAC is here to help. Contact us today to discuss your requirements and discover how our innovative solutions can support your production goals.
Get in Touch
For more information on our full range of capabilities, please complete the form below or contact our team directly on 0345 094 0993. At AFAC, we’re committed to pushing the boundaries of what’s possible with silicone rubber mouldings.