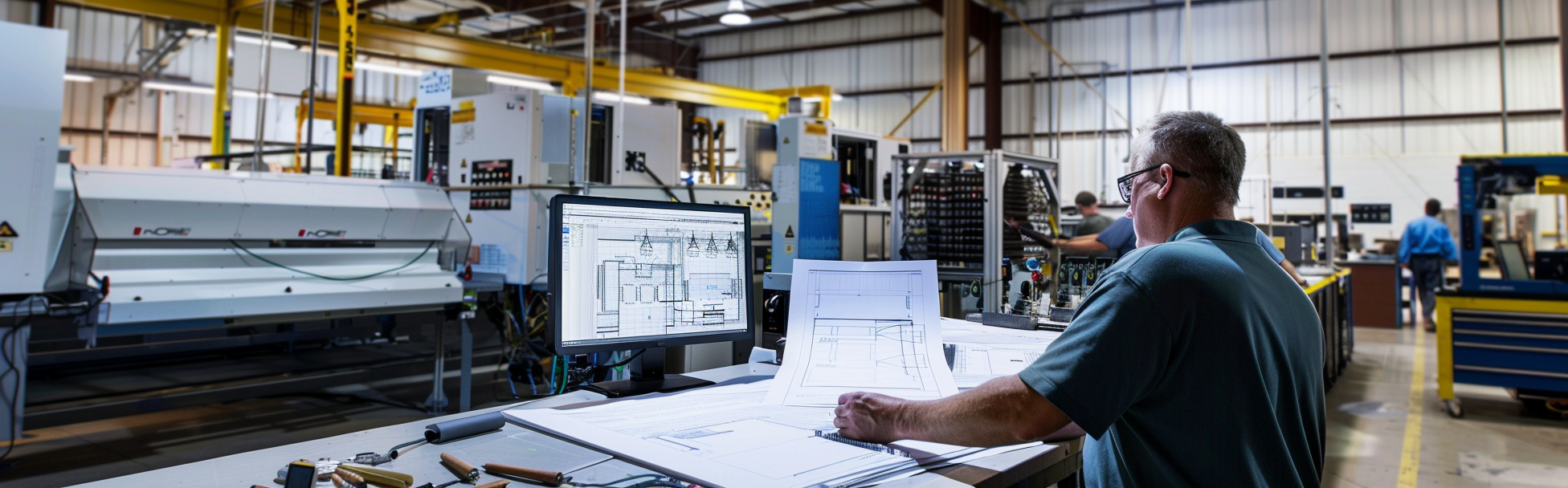
At AFAC, we pride ourselves on delivering custom solutions tailored to the unique needs of our clients. Recently, we had the opportunity to work with a prominent lighting manufacturer who required a bespoke part for their production line. This case study highlights our process, the challenges we faced, and the ultimate success of the project.
The Challenge
Our client, a leader in the lighting industry, approached us with a specific requirement for a blanking plug. This part needed to fit a particularly large hole in their assembly. The blanking plug also had to withstand high temperatures, as it would be exposed to powder-coating ovens during the manufacturing process. The client emphasized the need for a reliable seal around the edge of the hole and an easy method for removal.
Our Solution
Understanding the critical nature of this component, our team at AFAC designed a custom blanking plug made from high-quality silicone rubber. Here’s how we addressed the client’s requirements:
- Precision Fit: We engineered the blanking plug to fit perfectly into the specified hole. The seals were designed to ensure a tight, reliable fit around the edge, preventing any leaks or gaps.
- High-Temperature Resistance: The silicone rubber used in the plug is capable of withstanding temperatures up to 260 degrees centigrade. This ensures that the plug can safely go through the powder-coating ovens without degrading or losing its integrity.
- Ease of Use: We included a small handle on the plug, allowing for easy insertion and removal. This feature was particularly important for the client’s production team, as it streamlined their assembly process and reduced downtime.
The Results
Our custom blanking plug proved to be a perfect fit for the client’s needs. The precision of the seals and the high-temperature resistance of the silicone rubber ensured that the plug performed flawlessly in the production environment. The ease of use also received positive feedback from the client’s production team.
Client Feedback
The client was highly satisfied with the solution we provided. They praised the quality and durability of the blanking plug, noting that it significantly improved their production efficiency. The success of this project has strengthened our relationship with the client, and we look forward to collaborating on future projects.
Conclusion
This case study exemplifies AFAC’s commitment to providing tailored solutions that meet the specific needs of our clients. By understanding the challenges faced by our customers and leveraging our expertise in custom parts manufacturing, we deliver products that enhance production processes and contribute to the success of our clients.
If you are a quality manager, production manager, or product designer looking for custom parts to optimise your manufacturing process, AFAC is here to help. Contact us today to discuss your requirements and discover how we can support your business.
Get in Touch
For more information on our custom manufacturing capabilities, please complete the form below or contact our team directly on 0345 094 0993. We are always ready to assist you with your specific needs.