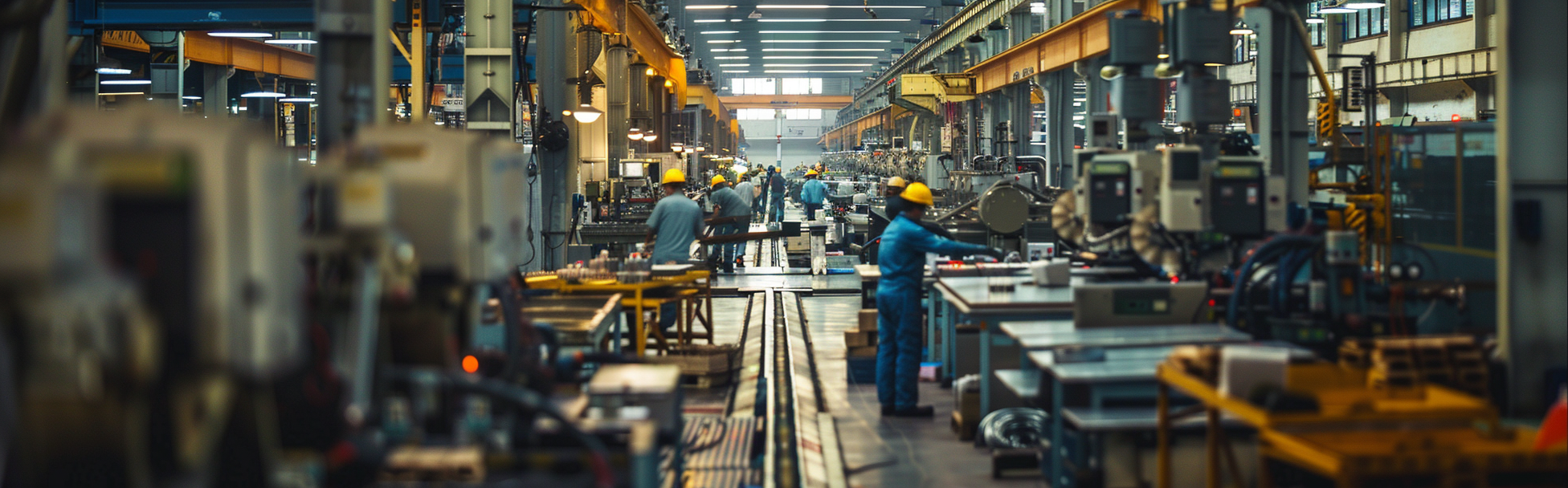
Welcome to AFAC Custom Masking Division! Today, we are excited to showcase an innovative plug designed to solve a specific masking challenge faced by one of our customers. This case study highlights how our tailored solution improved their production efficiency, precision, and cost-effectiveness.
The Challenge
The client, a manufacturer struggling with centering self-adhesive dots around holes during production, needed a more reliable and efficient masking solution. The primary issues were difficulty in achieving precise placement and the inefficiency of using self-adhesive dots, which often led to production delays and increased costs.
Our Solution
To address these challenges, AFAC designed a custom plug with the following key features:
- Comprehensive Masking: The plug effectively masks not only the hole but also the surrounding area, providing a more thorough solution than self-adhesive dots.
- Hollowed Back Design: The plug features a hollowed back, which reduces the amount of silicone used in its production, thereby cutting costs while maintaining functionality.
- Small Handle for Easy Removal: A small handle is incorporated into the design, ensuring that the plug can be easily inserted and removed, streamlining the masking process.
Implementation and Results
The custom plug was integrated into the client’s production line, leading to significant improvements:
- Enhanced Efficiency: The easy-to-use design allowed for quick and accurate placement, reducing production time and increasing throughput.
- Increased Precision: By masking both the hole and the surrounding area, the plug ensured precise coverage, improving the quality of the final product.
- Cost-Effectiveness: The hollowed back design reduced material costs, and the reusable nature of the plug further contributed to long-term savings.
Client Feedback
The client was extremely satisfied with the custom masking plug. They noted the substantial improvement in production efficiency and precision, as well as the cost savings achieved through reduced material usage and increased reusability. The ease of removal and placement was particularly praised for simplifying their workflow.
Conclusion
This case study exemplifies AFAC’s commitment to developing innovative and cost-effective solutions tailored to our clients’ specific needs. By addressing the challenges faced by the manufacturer, our custom plug enhanced their production processes and overall product quality.
If you are a quality manager, production manager, or product designer seeking custom masking solutions to optimise your manufacturing processes, AFAC is here to help. Contact us today to discuss your requirements and discover how our bespoke products can enhance your operations.
Get in Touch
For more information on our full range of capabilities, please complete the form below or contact our team directly on 0345 094 0993. At AFAC, we’re committed to pushing the boundaries of what’s possible with silicone rubber mouldings.